Resin floors are becoming famous lately! They provide a modern look to homes and commercial spaces. Here, we’ll discuss how to DIY a resin floor.
What is resin flooring? It’s a synthetic material poured on an existing floor to produce a shiny finish. There’s a variety of colors and styles for you to customize the floor according to your taste. Resin flooring is also durable, making it a great choice for high-traffic areas.
Before you begin, here are some points to consider:
- Prepare the existing floor. Clean it, and make sure it’s leveled and free from cracks.
- Select the right resin type. Epoxy resin or polyurethane resin each has its own properties and installation instructions.
Now, let’s move on to the step-by-step process of DIY resin flooring.
Did you know? Epoxy resin was first created by Dr Sylvan Oser in 1947. Initially, it was used for industrial purposes, but it’s now popular in residential settings too.
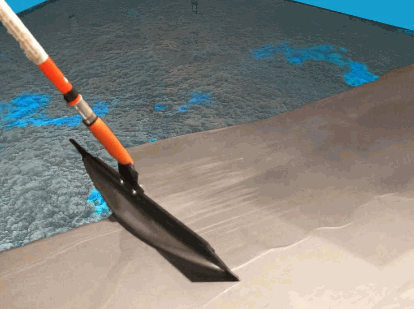
Understanding Resin Floors
Dive into the world of resin floors to learn their intricacies. From composition to application methods, nothing is left uncovered.
Resin floors are composed of epoxy or polyurethane resins, hardeners, and fillers. There are several types: epoxy terrazzo, self-smoothing epoxy, and decorative quartz systems.
The correct preparation of the substrate is a must before pouring the mixture, which needs time to cure.
Did you know that this type of flooring brings a seamless and hygienic solution to residential and commercial spaces? Plus, they are easy to maintain!
Remember: good ventilation during curing is essential for optimal results when installing resin floors.
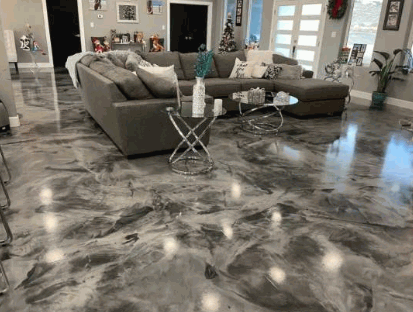
Materials And Tools Needed
Essential Equipment and Supplies
- Resin: Choose a high-quality epoxy resin that is suitable for the type of floor you are installing.
- Resin Hardener: This is necessary to activate the curing process of the epoxy resin.
- Mixing Tools: Use a drill with a mixing paddle or a mixing stick to thoroughly blend the resin and hardener.
In addition to these essential materials, you may also need additional items such as a putty knife, measuring cups, a squeegee, and a paint roller to assist with the application process.
It is important to note that the proper preparation and application techniques are crucial for achieving a successful resin floor.
Nobody knows resin better than a skateboarder with a clumsy streak – DIY your way to a floor that’s as smooth as you were in middle school.
Resin
Let’s explore the world of resin! A table displays its distinct properties.
Material | Properties |
Epoxy Resin | High strength & good adhesion. Used for laminating & coating. |
Polyester Resin | Low cost & fast curing. Commonly used in fiberglass manufacturing. |
Polyurethane Resin | Flexible & strong. Used for casting & making molds. |
Silicone Resin | Heat resistant & electrically insulated. Used in electronics & automotive industries. |
Did you know that resin can be mixed with pigments? And additives can be added to achieve special effects, like UV protection & shrinkage prevention.
Here are 3 tips to help you use resin in creative ways:
- Experiment with pigments for unique colors.
- Get creative with molds for depth & dimension.
- Prioritize safety – work in a well-ventilated area or wear respiratory protection.
Follow these suggestions to unlock the potential of this amazing material. Make your imaginative ideas come to life!
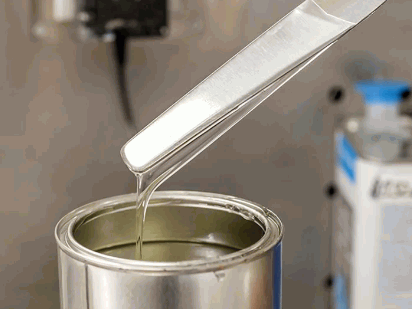
Hardener
Hardener is a key component of adhesives, coatings, and composites. When mixed with resin or epoxy, it triggers a chemical process called polymerization, forming a solid, rigid structure.
The amount of hardener used affects curing time and the material’s final physical properties. It helps to attain the desired hardness and resilience. Temperature sensitivity is also an important factor to consider when selecting the right hardener. Compatibility between hardeners and materials is crucial in industrial applications.
Surprisingly, hardener use dates back centuries. Ancient Egyptians used animal fat to harden construction materials, resulting in impressive architecture.
Thanks to science and tech, synthetic compounds have replaced many traditional hardeners, increasing performance and versatility.
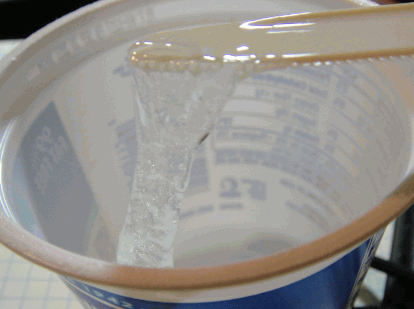
Pigments Or Dyes
Pigments or dyes? Optional – but get creative! Adding pigments or dyes to your project can give it an extra boost of visual appeal. These vibrant colors allow for eye-catching designs and patterns. Consider using pigments or dyes to add depth and character to your materials.
Let’s look at some practical examples. Cotton fabric? Blue and yellow for tie-dye t-shirts. Wood? Red and green for handmade wooden toys. Soap base? Pink and purple for DIY soap making.
Using pigments or dyes is optional – but it offers a great chance to get creative. Try out different shades and combinations to get the desired effect.
Did you know? Ancient civilizations used to extract pigments from natural sources – like plants and minerals. These precious colors were used to create amazing artworks that we still marvel at today.
So, the next time you start a creative project, consider exploring the world of pigments or dyes. Unleash your creativity and discover how colors can transform your crafts!
Check out: Can Epoxy Flooring Be Used On Wood
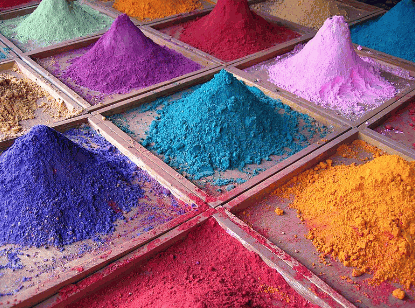
Protective Gear
Helmets – Protecting heads from impacts and safeguarding against head injuries. Safety goggles – Guarding eyes from debris, chemical splashes, or bright lights. Gloves – Safeguard hands from cuts, burns, or chemical exposure. Respirators – Filtering out harmful air particles and giving a clean breath during risky tasks. Earplugs – Lowering noise levels and protecting ears in loud places. Safety boots – Offering foot protection from falling objects or slippery surfaces.
It’s also essential to note that some activities may necessitate special gear tailored precisely to their risks and challenges.
Facts are facts: Wearing the right protective gear can reduce the risk of serious injury by up to 85%, according to the Occupational Safety and Health Administration (OSHA).
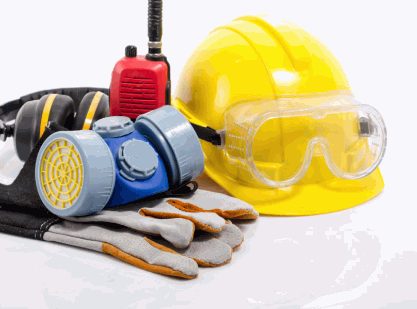
Preparing The Surface
To ensure proper adhesion and a smooth finish for your DIY resin floors, follow these steps:
- Clean the Surface: Remove any dirt, dust, or debris from the floor using a broom or vacuum cleaner.
- Repair Damages: Fill in any cracks, holes, or uneven areas with a suitable filler or patching compound. Smooth the surface with a putty knife and allow it to dry completely.
- Sand the Surface: Use sandpaper or a floor sander to roughen the surface slightly. This will help the resin bond better with the floor. Ensure you remove all dust after sanding.
- Prime the Surface: Apply a thin coat of primer specifically designed for resin floors. Use a roller or brush to evenly distribute the primer and allow it to dry according to the manufacturer’s instructions.
- Seal the Surface: Depending on the type of resin you are using, you may need to apply a sealer. Follow the resin manufacturer’s recommendations for the type of sealer and application method.
Keep in mind that each surface may have unique requirements, so it’s essential to follow the resin manufacturer’s instructions and consult professionals if needed.
For a successful floor installation, it’s crucial to properly prepare the surface for the resin application. Remember, a well-prepared surface will result in a long-lasting and visually appealing resin floor.
Say goodbye to your old floors and any shred of sanity you had left, because we’re about to embark on a DIY adventure that will make you question every life decision you’ve ever made.
Repairing Any Cracks Or Imperfections
Follow this 5-step guide to fix any cracks or imperfections!
- Check the Damage: Take a look at the surface for any cracks, chips, or other issues. Note their size and location to decide the best repair method.
- Clean Up: Clear the area around the cracks or flaws. Remove any dirt, dust, or debris with a brush or vacuum. Make sure the surface is dry and free from any contaminants.
- Add Filler Material: Choose a suitable filler based on the kind of surface and imperfection. For smaller problems, use spackling compound or wood filler. For bigger areas, use epoxy putty or mortar mix. Apply the filler with a putty knife, following instructions.
- Smooth and Level: Let the filler dry then sand it down with fine-grit sandpaper. Blend it in with the surrounding area for a seamless look. Wipe away excess dust with a clean cloth.
- Prime and Paint: After the repairs are smooth and perfect, apply primer to help the paint stick. Wait for the primer to dry then paint with the right techniques and colors.
Proper maintenance is key to avoiding future cracks and issues. Regularly check and repair any wear and tear quickly to keep surfaces looking great.
Follow these tips to repair cracks or imperfections and make sure they last long! Check out our range of repair products and make your space look stunning. Don’t miss out!
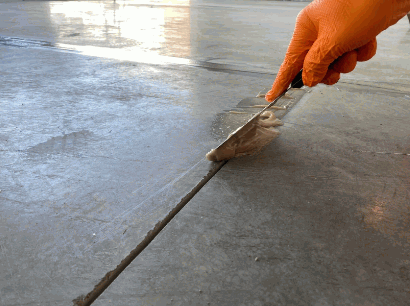
Applying The Resin
- Prepare the surface: Clean the floor thoroughly and make sure it is free from dirt, dust, and any other contaminants. Repair any damages or unevenness on the surface, and ensure it is completely dry before proceeding.
- Mix the resin: Follow the manufacturer’s instructions to mix the resin and hardener in the correct ratios. Use a clean bucket and stir the mixture gently but thoroughly to ensure a consistent blend.
- Apply the resin: Using a roller or a squeegee, spread the resin mixture evenly across the floor surface. Work in small sections to prevent the resin from drying before you finish applying it. Make sure to avoid any bubbles or uneven patches by using a roller or a brush to smooth out the surface.
It is important to note that the drying time and curing process will depend on the type of resin being used. Follow the manufacturer’s guidelines for the specific product you have chosen to achieve the best results.
For a flawless finish, consider applying multiple coats of resin and sanding between each coat for a smooth and seamless look. Remember to allow sufficient drying time between each coat.
Ensure proper ventilation during the application process and use protective gear such as gloves and a respirator to minimize exposure to fumes and chemicals. And finally, enjoy your beautiful, durable resin floors!
Don’t miss out on the opportunity to transform your floors with stunning resin finishes. Follow these steps and create a luxurious and modern look in your home or business. Start your resin flooring project today!
Mixing resin and hardener is like a recipe for disaster, but if you follow the instructions, you might just end up with a floor that’s smoother than a politician’s lies.
Mixing The Resin And Hardener According To The Manufacturer’s Instructions
Mixing resin with hardener is essential for success. Here’s how:
Step | Instructions |
---|---|
1 | Set up your work area with a protective covering. |
2 | Measure out the exact proportions of resin and hardener according to manufacturer instructions. |
3 | Pour the pre-measured resin into a clean container and scrape out every drop. |
4 | Then, add the correct amount of hardener. Be precise and avoid spills. |
5 | Stir the two components together with a stick or paddle. Make sure to mix out all streaks. |
Also, some manufacturers suggest stirring in a certain pattern for better results. Follow these guidelines for optimal outcomes.
Resin mixing has come a long way. Ancient civilizations used tree sap as resin. Today, modern measuring methods have revolutionized mixing techniques. This progress gives us resilient, visually stunning products in many industries and artistic pursuits.
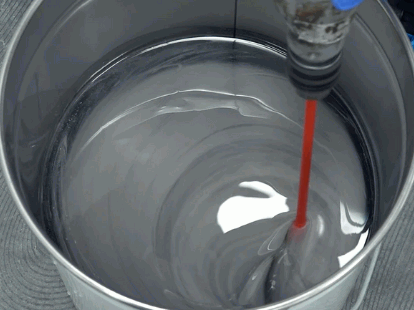
Applying The Resin Mixture To The Floor
- Clean and prep the floor: Vacuum or sweep away dirt, dust, and debris. Then use a mild detergent and water solution to remove any stubborn grease or stains. Allow the floor to dry fully.
- Mix the resin: Read the manufacturer’s directions, then mix the right amounts of resin and hardener in a clean container. Stir or blend until there are no streaks or lumps left.
- Apply the resin: Pour a small amount of the mixture into one corner and move to an exit point. Use a roller or brush to spread evenly over the surface. Be careful to cover all parts and work quickly so it doesn’t dry too soon.
Each type of resin may have different needs, so make sure to read and follow them. Don’t wait any longer – use this resin method to transform your space!
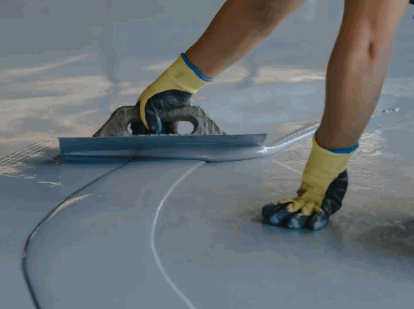
Use A Roller Or Squeegee To Spread The Resin Evenly
- Clean, dry, and clear the surface before you start.
- Pour the resin from one end and move across.
- Use a roller or squeegee to spread it evenly and apply even pressure.
- Do this in small sections to make sure you cover everything.
- If using a roller, cross the strokes slightly to avoid streaks.
- If using a squeegee, go in long, smooth strokes.
It’s important to use a roller or squeegee for better control and to avoid too much pooling. Moving at a steady pace and applying the same pressure will help you achieve an even finish. Read any special instructions for your brand or type of resin.
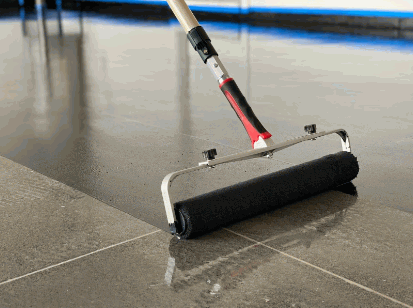
Adding Pigments Or Dyes
Adding pigments or dyes to your resin floors can enhance their appearance and create a unique decorative effect. Here are four key points to consider when adding colorants to resin surfaces:
- Selection of Pigments or Dyes: Choose high-quality pigments or dyes specifically designed for resin applications. Opt for colors that complement your space and match your desired aesthetic.
- Mixing: Start by adding a small amount of pigment or dye to the resin mixture and gradually increase until the desired color intensity is achieved. Mix thoroughly to ensure even distribution.
- Testing: Before applying the colored resin, it is recommended to conduct a small test patch to evaluate the color outcome. This allows you to make adjustments if needed and ensures the final result meets your expectations.
- UV Protection: If your resin floors are exposed to sunlight, consider using UV-resistant colorants to prevent fading or discoloration over time. This will ensure the longevity of your vibrant resin surface.
Achieve Stunning Results:
To create truly mesmerizing resin floors, experiment with different color combinations, layering techniques, or even the addition of metallic flakes. Let your creativity flow and design a space that reflects your unique style.
Pro Tip: When adding colorants to resin surfaces, always follow the manufacturer’s instructions and recommendations to achieve the best results.
Transform your dull flooring into vibrant works of art by adding pigments or dyes to the resin mixture – your guests won’t be able to resist twerking on these colorful masterpieces.
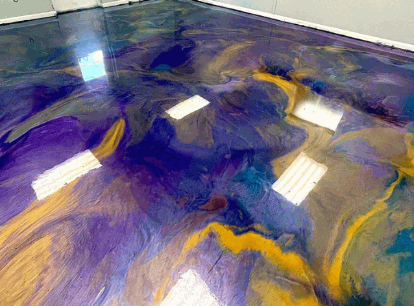
Adding Pigments Or Dyes To The Resin Mixture For A Desired Color
For resin art, choose high-quality pigments or dyes. These come as powders, pastes, and liquid tints. Consider the opacity and intensity of the pigment. Follow the manufacturer’s instructions for the mixing ratios. Make test swatches to see how the colors interact. Layer different colors to create depth and dimension. Compatible additives are crucial.
Nowadays, artists can mix multiple colors for unique creations. Jane Davenport even added crushed gemstones as pigments to her resin artworks. Unconventional materials give a touch of intrigue to resin art.
Mixing The Pigments Or Dyes Thoroughly
Mixing pigments or dyes is key for vibrant colors. Here’s how to get it right:
- Measure accurately. This is important for the desired intensity.
- Use separate containers. Avoid cross-contamination and maintain purity.
- Add slowly. Start with small amounts and increase till the desired shade.
- Mix well. Stir with a knife, brush, or mixer until blended evenly.
- Test for accuracy. Check a sample surface before committing to larger areas.
Detail is essential when mixing. Follow these steps and you can bring your creative visions to life! Got an idea? Get experimenting today and create captivating artwork that expresses your unique style!
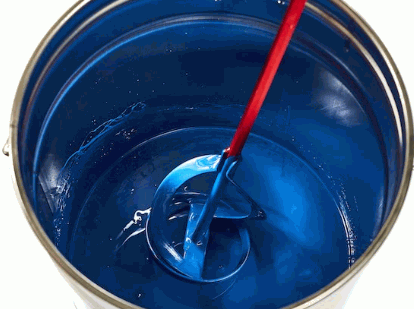
Applying The Colored Resin Mixture To The Floor
- Clean the surface carefully. Make sure no dust, debris, or grease could affect the adhesion of the resin.
- Mix the colored resin as per instructions. Ensure you have enough for the entire floor.
- Start pouring the resin in one corner. Move towards an exit point.
- Spread the resin with a squeegee or roller. Use long motions to avoid air bubbles or uneven spots.
- Let the colored resin dry as per the recommended time. Don’t touch or walk on it during this period.
Plus, remember: choose pigments or dyes made for resin flooring; wear protective gear like gloves and goggles; and multiple layers of resin for more durability.
Did you know? HomeAdvisor reported that pigments or dyes can increase the attractiveness and value of your property.
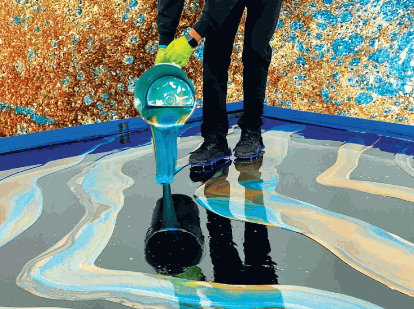
Curing And Finishing
Curing and finishing, also known as the final steps, involve the last processes in the DIY resin floor installation. These steps ensure that the resin cures properly and the floor achieves its desired finish.
To achieve the desired curing and finishing, it is important to follow the manufacturer’s instructions regarding the curing time, temperature, and environmental conditions. This will ensure that the resin hardens completely and creates a durable and long-lasting floor surface.
In addition to curing, finishing is an essential step in DIY resin floor installation. Finishing involves applying a protective topcoat to the cured resin to enhance its appearance and protect it from stains, abrasions, and UV damage. This can be done by using a clear, high-quality polyurethane or epoxy sealer. The sealer should be applied evenly and allowed to dry completely before the floor is ready for use.
Table:
Steps | Description |
---|---|
Step 1 | Follow the manufacturer’s instructions for curing time and temperature. |
Step 2 | Apply a protective topcoat to the cured resin, such as polyurethane or epoxy sealer. |
Step 3 | Allow the sealer to dry completely before using the floor. |
It is important to note that each resin product may have specific requirements for curing and finishing. Therefore, it is crucial to refer to the product’s instructions and guidelines to ensure proper curing and finishing of the DIY resin floor.
Interestingly, the practice of curing and finishing resin floors has a long history dating back to ancient civilizations. Early methods involved using natural resins and oils to protect and enhance the appearance of floors. Over time, advancements in technology and chemistry have allowed for the development of synthetic resins and specialized finishing products, making the process more efficient and effective.
By understanding and following the appropriate curing and finishing techniques, DIY enthusiasts can create beautiful and durable resin floors that will enhance the aesthetics of any space.
Don’t rush the curing process, unless you want your floor to look like a Picasso painting done by a two-year-old.
Allowing The Resin To Cure According To The Recommended Time
- Select a top-notch resin, then mix it according to manufacturer instructions.
- Spread it out on the surface.
- Let it be for the recommended curing time – don’t touch it!
- Monitor the resin and test it for hardness or flexibility.
Temperature and humidity can influence curing speed. Keep it in an area with the recommended ranges. Vapors released from some resins can be harmful, so work in a well-ventilated space or wear respiratory protection.
Remember these steps – allowing resin to cure is key to artistic success!
Applying A Topcoat Or Sealer For Added Protection And Shine
To get that perfect topcoat or sealer application, just do these three things!
- Prep the surface: Get rid of any dust or debris. Use a mild detergent solution and a cloth to clean. Let the surface dry completely.
- Apply the topcoat or sealer: Select the right product for your material. Use a brush, roller, or sprayer to evenly apply a thin coat. Follow instructions from the manufacturer.
- Allow drying time: Check the product label for the drying time. This guarantees the topcoat or sealer bonds well to the surface, giving you the best protection and shine.
Remember these details as well: find a ventilated area for application, use gloves and eyewear when handling chemicals, and mix the product properly before beginning.
Don’t miss out on that flawless finish – follow these steps carefully and add that extra layer of protection and shine to your project now!
Maintenance And Care
Resin floors require regular maintenance and care to keep them looking their best. Here are some important points to remember:
- Regular Cleaning: Clean your resin floors regularly using a soft mop or microfiber cloth to remove dirt and debris. Avoid using abrasive cleaners or tools that may scratch the surface.
- Spills and Stains: Wipe up spills immediately to prevent staining. For stubborn stains, use a mild detergent or specialized cleaner recommended for resin floors.
- Prevent Scratches: Place felt pads on the bottom of furniture legs to prevent scratches when moving them. Avoid dragging heavy objects across the floor.
- Periodic Maintenance: Depending on the level of foot traffic, it may be necessary to apply a fresh coat of resin every few years to maintain its appearance and protect against wear and tear.
In addition to these maintenance tips, it’s important to note that resin floors are not suitable for outdoor use or areas with excessive moisture. Proper care and maintenance will ensure the longevity and beauty of your resin floors.
Pro Tip: Place doormats at entrances to reduce the amount of dirt and debris that can be tracked onto your resin floors.
Resin floors are low maintenance, just remember to sweep away the bodies of your enemies regularly for that gleaming, pristine look.
Regular Cleaning And Maintenance Tips For Resin Floors
Regular cleaning and maintenance of resin floors is essential for them to last and look their best. Here are some tips to help you keep your resin floors in prime condition:
- Sweep or vacuum the floor regularly to remove any dirt or debris.
- Mop the floor with warm water and a mild detergent for routine cleaning.
- Avoid harsh chemicals or abrasive cleaners as they can harm the resin surface.
- Wipe up spills right away, especially acidic substances like vinegar or lemon juice.
- Put doormats at entryways to reduce the amount of dirt and grit tracked onto the floor.
- Apply a protective sealer often to increase the durability of your resin floor.
Be aware that some types of resin floors may need special care instructions. Always refer to the manufacturer’s guidelines for tailored maintenance advice.
Pro Tip: To maintain the glossy finish of your resin floor, use a non-abrasive microfiber mop for cleaning instead of regular brooms or rough brushes.
Conclusion
In brief, resin floors are ideal for DIYers aiming to refresh their space. Here are a few things to take into account:
- Durability: Resin floors provide a lasting option able to manage lots of foot traffic and regular use.
- Variety: With a great selection of colors and finishes, resin floors give you plenty of choices to fit any style.
- Low Maintenance: These floors need little care, making them perfect for hectic people or businesses.
- Cost-effective: Installing resin floors yourself can save you on labor costs, ideal for home improvement projects.
- Eco Advantages: Resin is eco-friendly and doesn’t release bad toxins, improving your indoor air.
On top of that, prepping well before applying resin is essential. Make sure the surface is clean, dry, and free from any pollutants to get the most out of it. Preparing properly will make sure your resin floor stays in great condition for many years.
Pro Tip: Before beginning your DIY job, try out resin on a tiny area or test piece to get used to the application process, and make sure you end up with the look you want.